当ブログ記事では機械・設備設計でよくやってしまう設計ミスや失敗についてまとめています。
とくに設計初心者は事前に読んでおき設計ミスを未然防止しましょう。
こちらの2つの記事は信頼性設計の考え方、検図の方法やポイントについてまとめています。
→ 設計ミスやトラブルを減らす信頼性設計の5原則
→ 検図は設計ミスやトラブルの最後の砦【寸法抜けや忘れを防ぐ具体策】
機械系の設計エンジニアにおすすめの資格を紹介しています。
→ 機械設計エンジニアにおすすめの資格は?【なりたい姿を想像しよう】
機械・設備の設計ミス、失敗事例集
わたしの設計経験において「あっ!! やっちまった!」という数々の実体験、ヒヤリハットをまとめました。
同じような経験のある人、心当たりのある人、多いと思います。
「あるあるだよね~」
とニヤけていただけたら幸いです。
特に機械設計初心者はここに挙げる代表的な設計ミスを事前に把握しておき、自分が設計するときに未然防止しましょう。
部品やユニットの干渉、衝突、接触
機械・設備設計で一番多いミス、かつ一番リスクが高いミスは部品の干渉や接触です。
組み立て時に発覚すると対象の部品を追加工、再製作が必要となるため納期やコストにも影響します。
機械設計者は「いかに干渉、接触を無くすか」について常に念頭におく必要があります。
3D-CADになって設計ミスによる干渉は減ってきた
わたしの自動機設計者時代は2D-CADが主流だったので、どうしても組立時に部品やユニットの干渉が発覚するケースが発生していました。
平面図、断面図で干渉有無を確認すると、やはり空間把握能力や徹底確認力、経験値が試されるます。
設計者によってもミスの発生件数に大きな差があったものです。
一方で最近の設計は設計構想段階や組立図設計、部品図作図(製作用に2Dも必要)、検図まで3D-CADで行っているので昔と比べて若手設計者も干渉の不具合件数が減っています。
3D-CADの方が空間をイメージしやすく多角的に見れるので、怪しい部分を重点的かつ手軽に確認しやすくなっていますね。
3D-CAD自体も進化してきており、Autodesk Inventorなどは干渉チェック機能も備わっています。
組み立て状態での干渉(稼働前での干渉)
3D-CADにて設計していれば見やすい部分なのですが、やはり正面、側面、上面と多方向からの確認を行うことで、発見することができます。
たとえ納期が迫っている時でも怪しいところは入念に確認しましょう。
(設備組み立て時に発覚したら余計に出荷納期に影響します)
大きな設備や自動機設計でユニットが分かれている場合、総組立図にした時にユニット同士が干渉していることに気が付かないこともあります。
個別ユニット設計が完了しても安心しないようにしましょう。
複数名でユニットを分担設計している場合などは特に注意が必要です。
隣り合うユニットの設計者と確認しましょう。
ユニット設計が完了してから図面データを提供するのではなく、定期的に情報共有、設計中CADデータ確認して情報共有しましょう。
その情報は統括設計者(取り纏め役)としっかりと共有しましょう。
可動する部品やユニットの干渉、接触
エアシリンダやモータ、その他アクチュエータの可動部分は必ずCAD上で稼働させましょう。
時間が無くても可動部は必ずCAD上でストロークエンドまで動かして確認します。
複数の動作が重複するユニットについても、この可動部分の接触確認時にプログラム上のインターロックが必要かどうか確認しておきましょう。
ベストなのは「プログラム、設備動作の動きに依らずに部品同士が干渉しない」状態です。
干渉、接触を未然に防ぐ対策について、まとめておきます。
- 必ず正面、側面、上面の多方向から確認(3D-CADがベスト)
- 部品同士だけでなく隣り合うユニットにも注意
- ユニット別に設計者が異なる場合は定期的に情報共有しコミュニケーション
- 統括設計者はすべての情報を把握する
- 可動部分は必ずCAD上で動かして干渉確認
複数人での設計であれば「定期的に情報共有すること」が何より重要です。
こちらの2つの記事は信頼性設計の考え方、検図の方法やポイントについてまとめています。
→ 設計ミスやトラブルを減らす信頼性設計の5原則
→ 検図は設計ミスやトラブルの最後の砦【寸法抜けや忘れを防ぐ具体策】
機械系の設計エンジニアにおすすめの資格を紹介しています。
→ 機械設計エンジニアにおすすめの資格は?【なりたい姿を想像しよう】
ボルトの頭、ワッシャを忘れてませんか?
こちらもよくある設計ミスで図面にボルトを書き込まないと後でボルト頭が接触してしまうことがあります。
何度この低頭ボルトに救われたことでしょう。
(→ 低頭ボルトはキャップボルトの頭の低いボルトです)
設備組み立て時にキャップボルトの頭が干渉して低頭ボルトを探したり、ワッシャが隣の部品に干渉して入らない為に小径ワッシャに変更すること、ありますよね。
組立現場はこの不具合に即対応すべく極低頭ボルト(一番キャップ頭が平たいヤツ)をあらかじめ在庫しているパターンもあります。(設計者は組立部門に頼っていてはいけません!)
このボルトやワッシャの干渉は設計時にボルトやワッシャのCADデータを入れないと発生します。
対策は「CADでの組立図の時点でボルトデータを入れる事」です。
設計ミスを防ぐために面倒がらずに書きましょう。
こちらのブログ記事では組立時によくやってしまう代表的なミス「タップ折れ」について書いています。復旧方法もあるので参考に。
→「タップが折れた! 原因と対策【折れたタップの取り方と対処方法】」
配線、配管の取り回し 可動部の配線や配管の動きは大丈夫?
意外と多いのが配線トラブルです。
配線、配管の取り回し 可動部の配線や配管の動きは大丈夫ですか?
配線、配管は曲線が多いことから、設計時に面倒でCAD上に記入しなかったりするとミスにつながります。
しっかりと配線の取り回しもCADデータに書きましょう。
配線や配管が短くて届かない、長すぎて邪魔
配線や配管の取り回し、長さの選定を組立者に頼っていませんか?
配線・配管の取り回しや長さは設計者があらかじめ決めておくべきです。
エア配管チューブは長さを組立時に決めてカットすることが容易ですが、規格コネクタの付いた電気配線は長さが規格で決まっています。
適当な長さを選定すると短くて届かなかったり、逆に長いと余ってしまい、丸めて束ねても邪魔になります。
設備の組立時に架台フレームやカバーフレームに配線を沿わせて引き回すと、当初の見込みよりも必要な配線長さが長くなることもあります。
組立時に配線長さが足りないと再購入やケーブルやコネクタの再製作となり、余計なコストとリードタイムが発生します。
機械設計時に配管や配線もCAD図面上に書きましょう。
可動部の配線と配管には特に注意が必要
可動部分の配線、配管が設備の動作によって可動する場合、配線が擦れて切れる、被覆が摩耗して芯線が露出する、漏電するなどのトラブルに発展します。
とくに細いセンサケーブルの摩耗やファイバセンサの芯線が折れてしまう不具合が多いです。
可動部は一日に何回動作しますか?
一か月で何回動きますか?
一年で何回ですか?
設計時になんとなく「大丈夫だろう」と考えても数か月や数年を考慮すると簡単に壊れます。
可動ケーブルは周囲との干渉を確認し、可動が頻繁な部分は対策としてケーブルキャリアを使いましょう。
購入機器の配管や配線取り回し方向は問題ないか?
使用する購入品の配管や配線の取り回しの方向にも注意が必要です。
それぞれの例を挙げておきます。
- エアシリンダであれば配管、センサケーブルの取り回し方向、スピコンやエルボの角度
- モータの給電、エンコーダ配線の取り回し方向
- 電動シリンダのモータ取り付け方向
- 近接センサやファイバセンサのケーブル方向、最小曲げ半径
購入品のCADデータをダウンロードして使用するときに、規格末尾の配線や配管の仕様が指定されていなかったり面倒で自分で想定しなかったりすると、組立時に干渉することがあります。
購入品CADデータを使用する時は必ず配管、配線、取り付け方向を確認し、型番末尾の情報が使用するCADに含まれているか確認しましょう。
ファイバセンサやエア配管の曲げ半径に注意
ファイバセンサを使用する場合、配線時の曲げ半径に注意する必要があります。
曲げ半径が小さいと中のファイバが折れてしまい、必要な光量が出力されなくなってしまいます。
エアシリンダのエア配管チューブも曲げ半径が小さすぎると折れてしまい、必要なエア圧が出なくなってしまいます。
配線、配管のスペースを考慮しないと、配線や配管が折れ曲げる事態が発生してしまうので、狭い部分にセンサやエアシリンダを取り付ける際は注意しましょう。
しっかりとCAD上に配線、配管の図面も書くことで、無理な配置に気が付くことができます。
こちらの2つの記事は信頼性設計の考え方、検図の方法やポイントについてまとめています。
→ 設計ミスやトラブルを減らす信頼性設計の5原則
→ 検図は設計ミスやトラブルの最後の砦【寸法抜けや忘れを防ぐ具体策】
機械系の設計エンジニアにおすすめの資格を紹介しています。
→ 機械設計エンジニアにおすすめの資格は?【なりたい姿を想像しよう】
購入品のCADデータは正しいですか?
最近は減ってきたのですが、こちらも”あるある”の設計ミスです。
購入品のCADデータを正しく自分の図面に反映できていない場合に発生する不具合です。
型番を入れるとCADデータの寸法が自動編集される業者が増えてきた
最近の部品業者のWebサイトで手に入るCADデータについて、規格型番を入力するとその部品のCADデータが自動編集されることが多くなりました。
若手機械設計者で知らない設計者も多いかもしれませんが、10年前はベースとなる型番部品のCADデータをダウンロードして、その2D-CADデータを自分で編集して使用していたものです。
例えばエアシリンダでΦ3の場合、Φ32シリンダの基本ストロークのCADデータをダウンロードしてから、自分が使用するストローク仕様に書き直す必要がありました。
シリンダ本体長さやシャフト長、シャフト先端部のオネジ長 or メネジ長 etc. これらが基本データと異なるので、自分でカタログを見ながら寸法を拾ってCADデータを編集します。
最近では選定した規格型番の入力→欲しい型番と全く同じCADデータがダウンロードできることがほとんどとなっており、うれしい限りです。
エアシリンダやモータのサイズ、取り付け寸法、シャフトやストローク長は注意
「選定した型番規格=全く同じCADデータ」がダウンロードできる場合は大丈夫ですが、対応していない部品メーカーのCADデータを使って設計する場合は気をつけましょう。
シリンダのCADデータ編集時の注意点については上述の通りですので、編集時に気を付けましょう。
サーボモータやステッピングモータについても、エンコーダ有無やブレーキ有無、配線の取り出し方向によってモーターサイズや取り付け寸法が変わることがあります。
ダウンロード時や自分でデータ編集するときには気をつけましょう。
こちらの2つの記事は信頼性設計の考え方、検図の方法やポイントについてまとめています。
→ 設計ミスやトラブルを減らす信頼性設計の5原則
→ 検図は設計ミスやトラブルの最後の砦【寸法抜けや忘れを防ぐ具体策】
機械系の設計エンジニアにおすすめの資格を紹介しています。
→ 機械設計エンジニアにおすすめの資格は?【なりたい姿を想像しよう】
設備が「組み立てできない」と恥ずかしいですよね
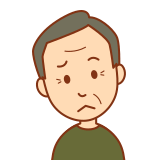
おい!! この部品、この形状だと組み立てできないじゃねーか!!
すぐ来い!!
我々の若手設計者時代は組立中の職人クラスの大先輩から電話でこのように呼び出されて、すぐに組立現場にCADノートパソコンを持って、すっ飛んで駆け付けたものです。
(心当たりのあるミドル設計者、多いのではないでしょうか?)
最近こんな厳しい人は少ないかもしれませんね笑。
厳しく正面から指導してくれる人が減っているとも言えるので少し寂しくもあります。
“なんとも言えない緊張感”があり、これが設計時や検図時の確認徹底に反映されていた面もありました。(過去に怒られた苦い経験による徹底確認力UP)
設備組立が自社ではなく委託業者の場合、もう少し「優しい感じで」問い合わせが来ると思います。
どちらにしても自分が設計した設備やユニットが「組立できない状況」は恥ずかしいです。
なにより納期に影響、修正コストも発生することを念頭に置かなければいけません。
こちらのブログ記事では検図の方法やポイントについてまとめています。
→「検図は設計ミスやトラブルの最後の砦【寸法抜けや忘れを防ぐ具体策】」
生産現場の低コスト効率化、設計力アップにおすすめの”からくり本”を紹介
→「からくり設計おすすめ本【生産現場のネタ探しと機械設計レベルアップ】」
機械系の設計エンジニアにおすすめの資格を紹介
→ 機械設計エンジニアにおすすめの資格は?【なりたい姿を想像しよう】
寸法間違い、穴位置ずれ など設計ミスによる組立不能
単純な寸法間違いや位置ずれは設計時の確認、検図における確認を徹底するしかありません。
3D-CADデータで組立図の確認を徹底しましょう。
2D加工図面の寸法抜けなど、自己検図も重要ですし、確認者による検図能力も重要です。
時々検図者を変えてみると、着眼点の違いから違った視点の指導をしてくれることもあるので設計スキルアップにお薦めです。
面取りやR加工忘れで部品が “奥まで組めない” or “入口でこじる”
2部品を組み込んで組み合わせる部分で、
- 穴部品の一番奥の内角Rが引っかかる
- 凸部品の先端角がC面取り加工されておらず、一番奥まで組めない
- 面取りが無くて入り口でこじる
といった事態が発生することがあります。
追加工で対応できますが、出戻り加工となり余計な時間とコストが掛かります。
しっかりと内角の逃がし加工、C面取りの加工を図面指示しましょう(検図でも確認しましょう)。
「分解できない」も基本的にダメです
分解できない=修理できないことを意味します。
設計者として「長く設備を使うことができる」ことを念頭に設計すべきですので、基本的に分解できない設計は避けましょう。
消耗部品の先端を溶接、厳しい精度が必要で強はめあい、など特殊な理由や目的が明確で、対応方法も決まっていればOKです。
はめあいの基本はH7g6 手感を覚えておこう
適性はめあい精度を把握していないため、設備組立時に摺動の修正が必要となることがあります。
これは機械設計製図便覧やJISに掲載されている「はめあい表」とそれぞれの感覚、手感を感じて覚えるしかありません。
はめあいの覚え方の基本はH7g6です。
“H7g6の手感の感覚”を自分の感覚基準として、それよりもキツくするか、緩くするか判断できるようにしましょう。
わたしの新人設計者の頃は、H7穴径部品とg6シャフト部品を組み合わせた一対のモデル製作部品を自分のデスク引き出しに入れていました。
設計時にこの部品を手感で確認しながら、
「もう少し硬い方がいいかな」
「もう少し緩い摺動にするかな」
のように都度イメージしていました。
頻繁に分解する必要があるのに「はまり込んで分解できない」とならないようにしましょう。
「調整できない!」 そんな機械・設備もNGです
よくあるミスとして「現場で調整できない」設備となってしまうことがあります。
単純に機械設計者のケアレスミス(調整を考えていない)の場合に加えて、設計者の想定と使用者の認識が違っている場合もあります。
単純に調整、点検、メンテナンスを考えていない設計
機械設計者として「使用する場合を想定した設計をする」ことは必須です。
購入部品、製作部品を積み木のように配置することが機械設計ではありません。
調整する、点検する、メンテナンスする、問題無くこれらが実施できることは必須です。
そのためのスペースや方法も考慮して設計しましょう。
六角レンチやドライバーなど、工具やゲージ類が入らない
調整、点検に使用する工具やゲージ類、測定機器が入るように(使用できるように)設計しましょう。
六角レンチの先端を短く切っていたり(私も短く切ったものを全種類揃えて持ってますが、、)、逆に長い方とメガネレンチの丸穴を使ったり、組み立てノウハウで切り抜ける場面もあります。
しかし基本的には設計時に特殊な調整方法、特殊な工具を必要としないことを念頭に設計しましょう。
ちなみに六角レンチの首下ショートの工具って売ってるんですね。
(私は昔、ディスクグラインダで自分で切断しました)
必要であれば購入しておいた方がいいでしょう(言っていることが矛盾してますね、、)。
手が入らない、体が入らない
海外に設備を出荷する時によくある事象です。
日本人をはじめ東南アジアの人種は小柄ですので、その標準想定で設計した設備を欧米に出荷すると、
「手が入らなくて調整できない」
「設備カバーが小さくて設備内部に入れない(身動きとれない)」
といったクレームになることがあります。
手の大きさ、身長の高さ、横幅、、かなり違うので注意が必要です。
日本人は特に手先が器用ですので、狭いところでも工具を動かせたり調整できてしまいます。
(六角レンチを片手親指でクルクル回せる人が多いですよね)
特に必要なスペースが限られている場合に自分の感覚で「このくらいの隙間なら調整できるかな」と考えていても、欧米の標準に照らし合わせると「狭くてできません」となってしまうことがあります。
海外向けに設備を出荷するときは調整スペースと余裕を確保して設計しましょう。
こちらの2つの記事は信頼性設計の考え方、検図の方法やポイントについてまとめています。
→ 設計ミスやトラブルを減らす信頼性設計の5原則
→ 検図は設計ミスやトラブルの最後の砦【寸法抜けや忘れを防ぐ具体策】
生産現場の低コスト効率化、設計力アップにおすすめの”からくり本”を紹介
→「からくり設計おすすめ本【生産現場のネタ探しと機械設計レベルアップ】」
機械系の設計エンジニアにおすすめの資格を紹介しています。
→ 機械設計エンジニアにおすすめの資格は?【なりたい姿を想像しよう】
電気、水、油、発熱が伴う機械・設備には注意
電気、水、油、熱を扱う設備や機械はとくに注意が必要です。
設計ユニット別に複数人の設計者が存在する場合など、別ユニットで使用されている特殊環境について把握していない場合があるので、統括設計者は注意しましょう。
電気が他機能に影響する可能性
内部基板や制御BOXについては機械設計者とは別に電気設計者が設計することもあると思います。
(自分ですべて設計する人もいますよね)
比較的大きな電流が流れる電源やケーブルが近くにあると、基板の電子部品が誤作動したりノイズ影響が発生することがあります。
ロードセルなど精密な電圧センサを使用しているとノイズ影響を受けやすいため、機器の配置や配線の取り回しに注意が必要です。
(ロードセルの配線は他の電流が大きい配線と一緒に束ねると、ノイズ影響が発生することがありるので分けて配線した方が無難です)
水配管がある場合は漏水に注意
機械設備に冷却水や給排水などの水配管がある場合、漏水に注意が必要です。
漏水した水が電気部分に流れるとショート、故障してしまいます。
製品に水が付着するのも問題ですね。
電気部品や基板などは設備上部に配置して水配管やタンクなどは設備下部に配置し、もしも配管から漏水しても電気関連部品や製品に水が掛からない(水が伝って流れない)ようにフェールセーフの設計をしましょう。
プレスなど冷却油や潤滑油も同じです。
アクチュエータの発熱、ワークの加工熱がある場合
アクチュエータを使用率の上限ギリギリで使用していたりすると発熱によってエラーが発生したり誤動作が発生したりします。
また連続で加工する設備の場合、加工時の発熱によって設備が高温になる場合もあります。
必要に応じて部品材料を熱伝導性の良い銅やアルミ材にして熱引けのよい放熱設計にしたり、冷却用のファンや冷却水配管を設置したり、冷却チラーを追加するなどの検討をしましょう。
発熱の可能性が予見されるか微妙な場合は、冷却機能をあとから追加できる構造にしておくとよいでしょう。
特殊用件は統括設計者から各ユニット設計者へ必ず情報共有が必要
隣り合うユニットの設計者が特殊用件を把握していない場合、その影響を受けて隣のユニットに不具合を発生させてしまう可能性が出てきます。
上記に挙げたような電気、水、油、発熱に関わる特殊用件がある場合、複数人で設計している時は必ず情報を共有しましょう。
国際規格に準拠しよう
日本はJIS、ヨーロッパはCEマーキング、アメリカはUL規格
最後に設計に関する「国際規格」についての認識です。
日本の機械設計、設備設計は基本的にJIS規格に準拠して設計していると思います(厳密に拘束する法律などは無いです)。
一方でヨーロッパはCE認証が無い設備の使用が許されていない為、ヨーロッパに設備を納入する際にはCE規格に準拠した機械設計、電気設計が必要です。
アメリカはUL規格への準拠が必要です。
設備や機械に使用する個々の部品すべてについてCE認証やUL規格が求められているわけではありません。
具体的な対応については欧米向けで特殊な対応が必要になることが多いため、事前に専門家に確認をしながら必要となる要件を確認して進めましょう。
検図を徹底して設計ミスを早期発見
今まで設計ミスをしないためのコツやポイントについて説明してきました。
最後に言いたいのは「設計ミスを見つける」ことの重要性です。
どんなに優れた設計者でも、設計規模が大きかったり、納期が短かったり、様々な要因が重なった場合、設計時には気が付かないミスや見落とし、忘れが発生してしまう事は避けられません。
自分で検図を徹底し、設計ミスを見つけ出して対処することが必要です。
具体的な方法・視点について、こちらで紹介しています。
→「検図は設計ミスやトラブルの最後の砦【寸法抜けや忘れを防ぐ具体策】」
検図の方法やポイントを理解して設計ミスの流出防止を強化しましょう。
以上、機械設備の設計ミス、よくやってしまう失敗事例についてでした。
設計初心者は今回紹介した代表的な機械設計の不具合や”あるある設計ミス”の事例と対策を事前に把握しておき、「やっちまった!」とならないように未然防止しましょう。
こちらの2つの記事は信頼性設計の考え方、検図の方法やポイントについてまとめています。
→ 設計ミスやトラブルを減らす信頼性設計の5原則
→ 検図は設計ミスやトラブルの最後の砦【寸法抜けや忘れを防ぐ具体策】
生産現場の低コスト効率化、設計力アップにおすすめの”からくり本”を紹介
→「からくり設計おすすめ本【生産現場のネタ探しと機械設計レベルアップ】」
機械系の設計エンジニアにおすすめの資格を紹介しています。
→ 機械設計エンジニアにおすすめの資格は?【なりたい姿を想像しよう】
コメント